RV10 MULTIMASTER
The new RV10 Multimaster enables high-volume production in the diameter range of 2-13 mm.
To this end, all stations are fully CNC-controlled and offer machining from three sides with powerful spindles or high-frequency drives. In addition, the large chip spaces enable optimum machining of long-chipping materials. Another positive factor is the clearly visible machining area, which offers the best possible accessibility and thus simplifies machine setup. During the development of our new machine type, the focus was on visual ergonomics to ensure user-friendly operation.
A new touch concept has been implemented for a high level of operating convenience. Touch operation enables simple navigation through the menus and a great overall overview. All information on the current process is displayed at a glance. The machine informs you whether processing has already started, is in progress, has been completed or whether a fault has occurred. There is also a status message that provides information on the current status of the machine. Another highlight is tool management. Among other things, the system provides information on how long the tools have been in use, their service life, the time remaining until they need to be changed and any increased wear or tool breakage. To maximize safety, there are additional mechanical buttons for motion control. Movement and function confirmation is always carried out via safety buttons in a clearly defined haptic area.
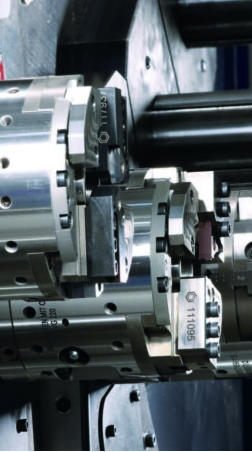
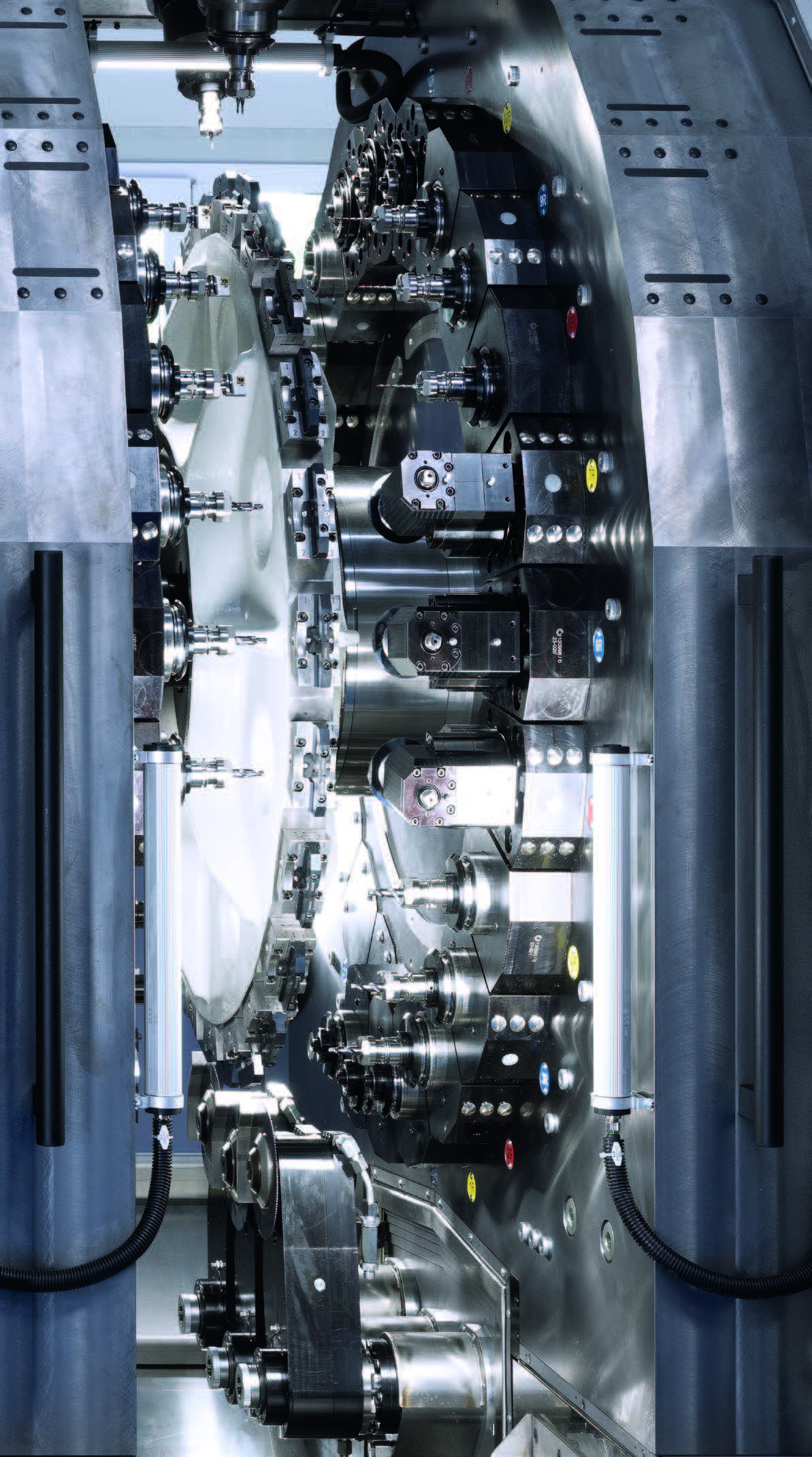
The machine concept of this system combines the cycle times of a cam machine with the flexibility of a CNC machine. With its 24 stations, the RV10 Multimaster is designed for triple processing. It is practically three machines in one, with independent production lanes and the option of running different output cross-sections. One coil per track is fed in parallel. The patented Winema Front spindle unit can be used on all three tracks. If required, a grooving or turning operation can be carried out before the workpiece is clamped in the clamping plate so that the outer contour – or parts of it – can be machined, which then lie in the clamping area. Alternatively, pressed parts or cast or sintered parts can be fed into the machine.
For highly complex parts, the production concept can be designed as 2-track machining. Depending on requirements, the machine can be equipped with up to 22 axial and 3 radial machining units per track.
Technical data
Max. Material diameter rod Ø 2-13 mm
Item 16 mm
Max. Workpiece length 80 mm
Clamping stations 24
Output per minute up to 200 pieces
Machining units Max. 54 (45 axial, 9 radial)
Stroke of machining units 90 mm
Clamping system centrically clamping 2-jaw chuck
CNC control unit Bosch XM 42
Quill feed
Weight (depending on equipment) 27,000 kg
Further advantages of the RV10 Multimaster result from the ability to process different workpieces at the same time and to ensure that other machine groups are relieved and that single-track machines are temporarily relieved. The machine system can act as a backup solution for individual machines in high-volume production, offering you a high degree of flexibility and safety to minimize downtimes and maintain your productivity.