- Offer Profile
- Customer satisfaction is our main motivation for continuously improving our
products and adapting to the challenges of the market. Our company
specializes in a few core tasks, such as laser-cutting for plastic
components, clip assembly in plastic components, automatic adhesive-strip
application and compact cells for a wide variety of assignments.
Product Portfolio
PRODUCT OVERVIEW
- Our product range focuses on several core areas. This
allows us to optimize the systems so that our customers can enjoy the most
cost-effective production processes possible.
Because of the special requirements for our products, we produce a large
share of the systems ourselves. As a result, any
in-house innovations, customer suggestions and experiences feed directly
into our systems. For purchased parts, we exclusively use
components from long-time suppliers with the highest quality standards.
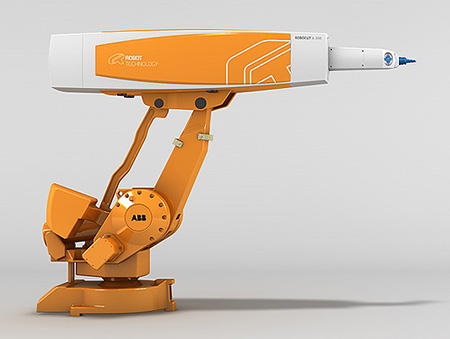
LASER-CUTTING ROBOT
ROBOCUT SERIES
- The ROBOCUT laser robot is the ideal device for
processing plastic components and thin metal sheets.
- Outstanding component accessibility
- Reliable and economical
- Laser power of 100 - 1000 W
There are several laser robots on the market, but this
unique combination of laser and robot is only available from
ROBOT-TECHNOLOGY. This combination provides the ideal tool for processing
plastic and metal components.
The machine is based on an IRB 4400 ABB robot, with the patented laser axis
mounted on it.
The laser robot comes with a laser power ranging from 100 – 1000 W in order
to meet your various needs.
The main area of application for the laser robot is cutting plastic molding
components for automobiles, such as pillar coverings, door modules, trunk
linings and exterior covering components. It can cut almost any type of
plastic, such as PP, PE, ABS-PC, Plexiglas and TPO films, as well as all
kinds of textiles – with the best cutting quality and speed. Combination
materials are ideally suited for processing with the laser robot. It can
economically process steel panels up to 3 mm thick, and stainless-steel
components up to 2 mm. The unrivaled flexibility of the laser robot offers
you new possibilities for processing components.

LASER-CUTTING SYSTEM
FLACS RT C-SERIES
- This system represents the latest technological
developments, making it the perfect foundation for processing your
components.
- Integrates all of the components into one system
- Short intervals due to the patented turntable
- Compact system structure
- User-friendly system controls
With the FLACS RT C-Series laser-cutting system, we
became the world’s first company to introduce a system that combines all of
the necessary components into a single unit with an exceptional design. The FLACS RT-Series
laser-cutting system uses our proprietary ROBOCUT laser robot. The laser
robot can be equipped with an integrated CO2 laser, with output between 100
– 1000 W, a CO2 laser with an external laser-beam arm up to 2 KW, or a fiber
laser up to 2 KW.

LASER-CUTTING STATION
FLACS SCAN 300/600
- A standard laser station for cost-effective processing of
plastic components. This flexible system provides an interesting alternative
to conventional stamping.
- Processing very precise contours
- Fast processing speeds
- Cutting, marking, perforation and machining
By minimizing the mass being moved (the laser beam
is diverted using two very lightweight mirrors), it allows extremely precise
contours to be created at very high speeds. In addition to cutting
components, you can also mark, perforate and machine materials. The level of
precision is up to +/- 0.02 mm, depending on the application.
This system concept uses CO2 lasers with a laser power between 60 and 300 W.
The laser is mounted on an adjustment plate and equipped with a completely
sealed beam guidance system, which is kept free from dust through
overload pressure.

LASER-CUTTING STATION
FLACS SCAN 100
- A standard laser station
for cost-effective processing of plastic components. This flexible system
provides an interesting alternative to conventional stamping.
- Processing very precise contours
- Fast processing speeds
- Cutting, marking, perforation and machining
By minimizing the mass being moved (the laser beam is
diverted using two very lightweight mirrors), it
allows extremely precise contours to be created at very high speeds. In
addition to cutting components, you can also mark, perforate
and machine materials. The level of precision is up to +/- 0.02 mm,
depending on the application.
This system concept uses CO2 lasers with a laser power between 60 and 300 W.
The laser is mounted on an adjustment plate and equipped with a completely
sealed beam guidance system, which is kept free from dust through overload
pressure.

LASER MARKING UNIT
FLACS MARK
- This newly constructed marking unit was specially
developed for applications in the plastics industry.
- Durable, high-quality markings
- Windows-based system is simple to program and use
- Cutting, marking, processing …
In particular, the development
process focused on a compact structure, a high level of flexibility and a
high rate of availability for raw industrial use. Although all of the
development goals were fulfilled, we were also able to keep the price within
an attractive range. As a result, our marking unit offers an ideal
alternative to other marking processes.
Laser marking guarantees high-quality, flexible and durable marking for your
components. You can automatically use the existing sequential production
numbers, the date and production time when labeling components.
The system is programmed and operated through a touchpanel PC, using our
proven standard user interface. The Windows-based interface guarantees that
it is simple to use.

SCANNER SOFTWARE
SCAN GRID
- This software is optimally designed for tasks involving
laser cutting
and laser pitching. The software allows free-form contours to be
programmed right at the component, the same way as with a robot.
- Compatible with robot control and system controls
- Adjustments can be made quickly and cost-effectively according to customer requests
This results in
simple, fast and precise programming. The software has special features for
laser pitching, for instance allowing you to fill predefined fields with
pitch points in a freely definable grid. Individual points can also be
deleted at positions where pitch points are not permissible. This feature
saves a significant amount of time in comparison to other scanner programs.
Another advantage of our proprietary software is its compatibility with the
robot control and systems controls.
Because we developed it ourselves, it is easy to make adjustments at any
time based on customer requests – quickly and cost-effectively.

LASER PERFORATION
- Laser
perforation is becoming increasingly popular; it is used in the automotive
industry to create vacuum holes and airbag perforations.
- Pinpoint or partial perforation
- Highly precise and fast
- Includes a monitoring system and product documentation
Our ROBOCUT laser robot, with its corresponding switching
electronics to control the laser, and our FLACS.SCAN laser-cutting
system can be used to monitor and document the laser work online.

REMOTE WELDING SYSTEM
FLACS RWS
- The FLACS RWS system is a large-scale remote system that
uses a mirror driven by two axes to very quickly position a high-performance
laser beam on a component. This allows metal components to be welded very
precisely and quickly.
- Laser power up to 8 kW
- Suitable for integrating CO2 lasers and fiber lasers
- Highly dynamic drive unit
The FLACS.RWS remote welding system is the ideal basis for welding metal
components. Laser power of up to 8 kW can be used. The system is suitable
for integrating CO2 lasers and fiber lasers.

INJECTION MOLDING AUTOMATION
- We exclusively use
6-axis robots to remove components from injection molding systems. These
robots guarantee a high level of flexibility and precision.
These shelf-type robots, which have now been successfully established on the
market, can be assembled on top of the injection molding machine to save
space. Removal from the injection molding machine takes place from above, as
with conventional linear robots.
Advantages:
- High level of flexibility with 6-axis robot
- High level of precision and fast processing
- Place-saving design with shelf robot

SYSTEM SOLUTIONS
- Increasing cost pressure in the industry is requiring
more and more complex automation solutions. Particularly with these
comprehensive solutions, ROBOT-TECHNOLOGY’s many years of experience are a
valuable asset.
- Sample application: trunk lining
- Sample application: windowsill for Golf A5
- Sample application: adhesive-strip application
- Sample application: aquarium assembly

COMPACT SYSTEMS
- More and more often, our customers are asking for
automation systems with a compact structure. Our many years of experience
allow us to create and implement an extremely compact structure even during
the design phase. Standard components are combined modularly to create
systems for a wide variety of tasks.
- Clipping and adhesive application
- Ultrasonic welding
- Laser cutting
A small footprint and short delivery times are the most common requirements
that our customers have for automation systems. In order to meet these
requirements, we developed a modular system of compact machines for a
variety of application areas. Tasks like clipping, applying adhesive,
ultrasonic welding and laser cutting can all be realized using this system.
SAMPLE PROJECTS
- ROBOT-TECHNOLOGY specializes in building systems for
manufacturing automotive components. Our customers manufacture a wide range
of interior and exterior components using our systems. The following
overview shows examples of some of these components.

A/B/C PILLARS
- One of ROBOT-TECHNOLOGY’s specialties is laser-cutting
pillar coverings for motor vehicles. These components, made with back
injection molded materials, must be cut very cleanly and precisely after the
injection molding process. They require a high level of path accuracy and a
clean, smooth cut features that are guaranteed by our laser robot.
ROBOT-TECHNOLOGY’s complete system solutions ensure a high level of process
security and fast applications.

FILMS
- The back injection molding process for film components is
gaining popularity in the automotive industry. Before the injection process,
the film is cut using laser systems from ROBOT-TECHNOLOGY. It is important
for this process to be clean and extremely precise. ROBOT-TECHNOLOGY’s
scanner technology, combined with the laser robot or the FLACS.SCAN,
guarantees these characteristics. In addition, we have built up a wealth of
expertise in the area of fixture building, which is combined with vacuum
technology to form the basis for this process.

BUMPER
- In processing automotive bumpers, ROBOT-TECHNOLOGY offers
systems for removing the bumper from the injection molding machine as well
as laser systems for cutting the different variants. Shelf-type robots are
often used for removing parts from the injection molding machine; they also
perform follow-up tasks, such as sprue cutting, flaming, creating variants,
etc. The laser-cutting systems produce various chrome liner versions,
license-plate designs, cutouts for exhaust-gas cleaning systems and hitch
fittings. The advantage is that the different variants can be realized in a
highly precise way after painting, and without post-processing.

I-PANEL
- The processing of I-panels involves various tasks. With
our laser systems, ROBOT-TECHNOLOGY allows for edge cutting, cutouts in the
center area and airbag perforations.

TRUNK LINING
- A significant application area for laser-cutting systems
is cutting the linings for car trunks. The rear injection molded carpet
needs to be cut perfectly to size. Often, this also involves cutouts for CD
players, GPS systems, etc. Our systems are highly flexible in this area.

STEERING WHEEL
- Laser-cutting systems from ROBOT-TECHNOLOGY are used in
creating variants of steering wheels. Laser cutting allows for
cost-effective realization of highly flexible components that do not require
post-processing.

HEADLIGHT HOUSING
- Our FLACS.SCAN laser-cutting system is an optimal
processing system for creating variants of headlight housings. Our systems
technology also guarantees a high level of precision in hard-to-reach areas.
Stamping equipment would not be suitable here because of the complex angles.

MIRROR HOUSING
- Injection molded mirror housings are removed by 6-axis
robots. Here our systems offer a high level of flexibility, fast removal and
a high level of process security.

REAR WINDOW SHELF
- In general, rear window shelves with fabric decorations
cannot be processed using stamping equipment. Stamping equipment is not
flexible enough, and it does not make clean cuts. Laser systems allow these
components to be manufactured with a high level of precision and without
filament formation.

TELEPHONE COVER
- The FLACS.SCAN laser-cutting system is optimal for
cutting films, for instance to be used with telephone covers. Our systems
allow you to achieve shorter intervals and higher quality standards than
ever before.

SEPARATION WALL / TRUNK
- The plastic components, back injection molded with needle
fleece, are processed with laser-cutting systems from ROBOT-TECHNOLOGY.
For instance, our systems execute the edge cutting and the cutouts for
creating variants. The advantage is a very clean, precise-edged cut.

DOOR MODULE
- In processing door modules, ROBOT-TECHNOLOGY offers
systems for a wide variety of components. For instance, we can perforate
windowsills in order to allow later vacuum sealing, cut door inserts for
later welding, and process back injection molded arm rests with precise
edges. For these components, a clean, smooth cut is essential for later
high-quality use.

DOOR MODULE PITCHING
- In a subsequent process, door modules are covered by a
film. This requires vacuum holes to be made. The vacuum holes are created
very quickly and precisely using our FLACS.SCAN laser-cutting system.
The holes have a very small diameter and are no longer visible after they are covered. The laser
process also makes it possible to avoid burr formation.

CYLINDER HEAD GASKET
- Cylinder head gaskets manufactured with a metal-rubber
composite usually need to be cut after the injection process.
ROBOT-TECHNOLOGY’s FLACS.SCAN laser-cutting system is used here to guarantee
fast, highly precise cutting. A simple reprogramming process allows a wide
variety of variants to be cut in a very short amount of time.